L’usinage CNC est largement utilisé au sein de différentes industries pour sa haute précision, sa vitesse, son efficacité et sa capacité à produire des pièces d’une grande exactitude. Cependant, comparés à d’autres méthodes de fabrication (comme l’imprimerie 3D), les services d’usinage CNC peuvent aussi être plus coûteux. Naturellement, le coût est un facteur prépondérant dans les applications d’usinage CNC, et cela aussi bien dans le cas de la fabrication d’une pièce unique que d’une production de masse en grande série. Cet article énonce 10 astuces qui vous permettront de réduire significativement les coûts de vos pièces mécaniques usinées en CNC.
Quels facteurs ont le plus d’impact sur les pièces usinées en CNC ?
Avant même de chercher à réduire les coûts d’usinage, il est important de comprendre par quels facteurs ces mêmes coûts sont affectés. La liste ci-dessous présente les quatre facteurs dont dépendent les frais d’usinage CNC :
- Coûts de mise en place : ces coûts recouvrent tout ce qui va de la préparation des fichiers CAD ou CAM, jusqu’à la planification du processus de fabrication. Les frais de mise en place sont fixes mais ont un plus gros impact dans le cadre des productions à faibles volumes.
- Coûts des matériaux : le coût des matériaux à partir desquels les pièces sont fabriquées affecte le coût global du processus de fabrication (sans parler du prix du produit fini) de façon significative. Des matériaux rares peuvent rapidement faire monter les prix. L’usinabilité du matériau choisi est aussi un aspect à prendre compte car il affecte le temps et l’effort, ainsi que les ressources, à consacrer à la fabrication.
- Temps d’usinage : dans le monde de l’usinage CNC, le vieil adage « le temps c’est de l’argent » prend tout son sens. Plus une pièce aura besoin de temps pour être usinée, plus le montant de la facture sera élevé, car les coûts impliqués (maintenance et opération des machines, consommation d’énergie, salaire des opérateurs) sont directement fonction du temps d’usinage.
- Frais divers : ces coûts recouvrent tout ce qui peut être considéré comme des exigences spéciales ou additionnelles. On peut citer par exemple : des tolérances très serrées, un outillage spécifique, des contrôles qualités plus exigeants ou une vitesse d’usinage diminuée.
Maintenant que nous sommes familiarisés avec les facteurs qui influencent le plus les coûts d’usinage CNC, nous pouvons formuler différentes façons de les réduire.
10 astuces pour réduire le coût de vos pièces mécaniques usinées en CNC
En regardant de plus près les différents facteurs qui influencent les coûts de l’usinage CNC, on peut extrapoler trois principales manières de les réduire : l’optimisation du concept, le choix des matériaux et d’autres considérations particulières. Parmi ces trois items, l’optimisation du concept demeure le plus important. Ci-dessous vous trouverez dix méthodes qui vous permettront de réduire significativement vos coûts d’usinage CNC.
1. Le choix des matériaux
Avant de jeter votre dévolu sur un matériau particulier, renseignez-vous de façon approfondie afin de vous assurer qu’il s’agit de l’option la moins onéreuse remplissant toutes les exigences de votre application. Il ne s’agit pas de faire des compromis sur la qualité, mais il est possible que certaines propriétés d’un matériau ne soient nécessaires dans le cadre de votre application. Par exemple : un acier résistant à la chaleur est tout à fait superflu (et onéreux) quand il s’agit d’usiner un sifflet.
Un autre critère à prendre en compte quand on choisit un matériau est son usinabilité. Certains matériaux, comme l’aluminium, sont très aisés à usiner et, en l’absence d’exigences particulières, devraient être l’option par défaut. Le coût peut cependant varier selon les alliages d’aluminium. Par exemple, l’aluminium 3.1645, plus rare, augmentera le prix d’une pièce mécanique de 25% en moyenne par rapport à l’aluminium 3.3206.
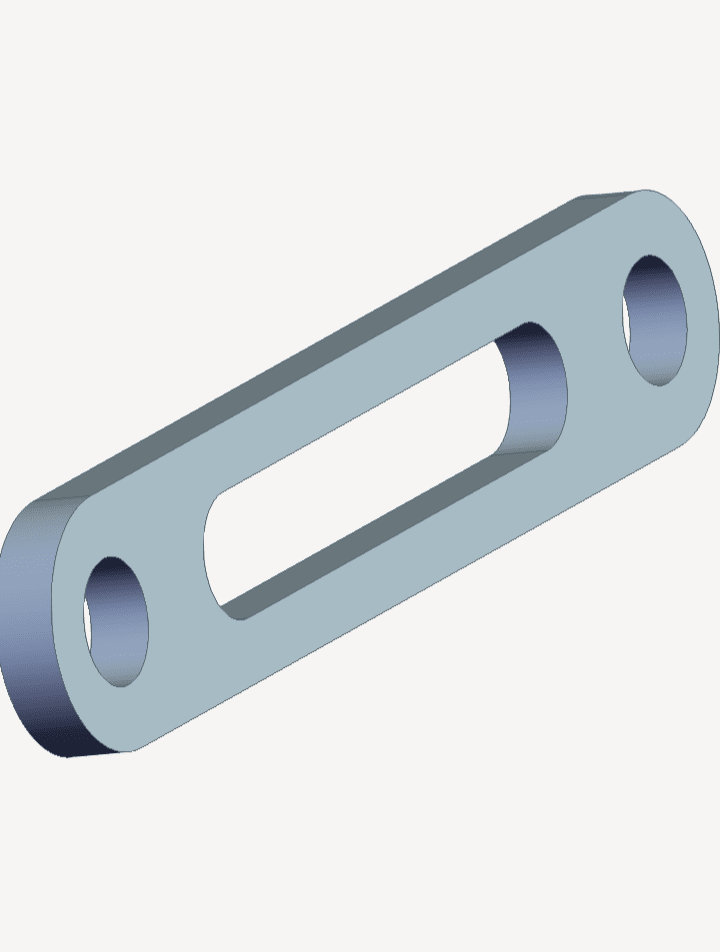
2. Éviter les traitements surnuméraires
Les pièces produites par usinage CNC présentent généralement un grain de surface satisfaisant tel quel. Bien que parfois nécessaires, des traitements de surface supplémentaires sont plus chers à appliquer. Par conséquent, certains traitements, comme l’anodisation ou les revêtements chimiques, ne devraient être employés qu’en cas d’absolue nécessité. Une autre façon de réduire les coûts consiste à conserver un traitement de surface uniforme sur toute la pièce. Appliquer un microbillage sur une partie d’une pièce et un revêtement chimique sur une autre partie aura tendance à gonfler votre facture.
3. Commander en gros
Les principes de l’économie d’échelle s’appliquent remarquablement à l’usinage CNC : les coûts ont tendance à diminuer de façon exponentielle avec l’augmentation des volumes. Pour mettre les choses en perspectives, produire la pièce représentée sur l’image ci-dessous en un seul exemplaire coûtera €30.75. À partir de 10 pièces, le prix tombe à €9.62. Et pour 100 pièces, on est à €6.76. La raison en est que les coûts de mise en place restent les mêmes, et cela que l’on produise 1 ou 100 pièces. Les commandes en gros permettent aussi d’éliminer les coûts de mise en place sur différentes machines, étant donné que la même configuration sera utilisée pour l’ensemble de la production. Profitez donc des avantages offerts par l’économie d’échelle en commandant en gros.
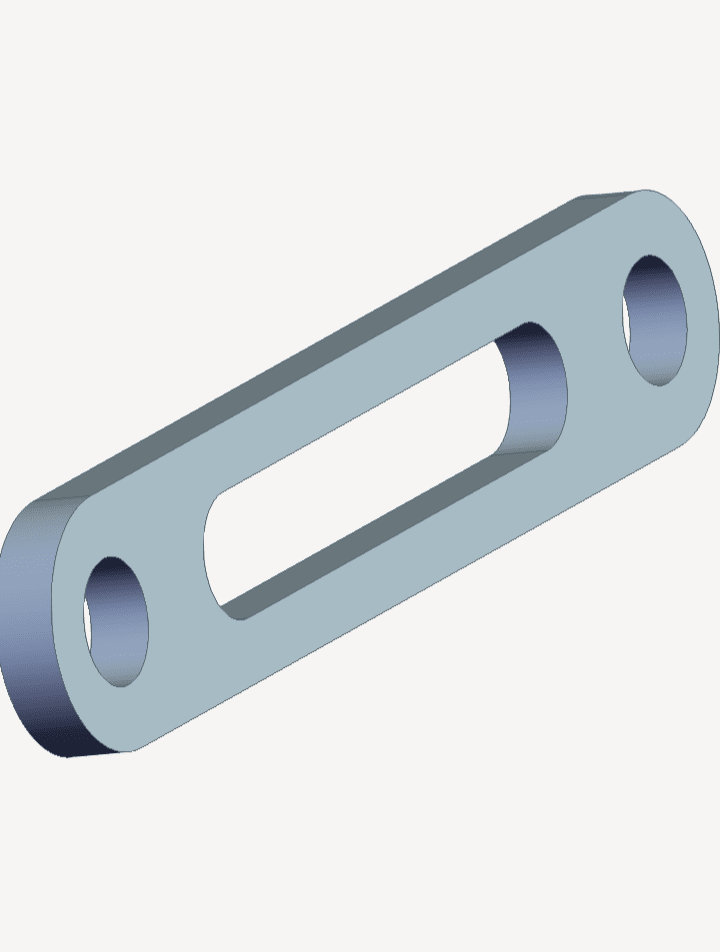
4. Eviter les parois excessivement fines
En raison de leur fragilité, les parois fines ont besoin de plus de temps pour être usinées car elles doivent être usinées en plusieurs étapes, à des profondeurs de découpe réduites. Elles ont également une fâcheuse tendance à vibrer, ce qui rend leur usinage en fonction des tolérances spécifiées particulièrement délicat et chronophage. Les temps d’usinage s’en trouvant accrus, les coûts associés augmentent. Pour éviter cela, assurer vous que vos parois aient une épaisseur appropriée : nos recommandations précisent que l’épaisseur minimale d’une paroi en métal est de 0,8 mm. Dans le cas d’une paroi en plastique, il ne faudra pas tomber en dessous de 1,5 mm d’épaisseur.
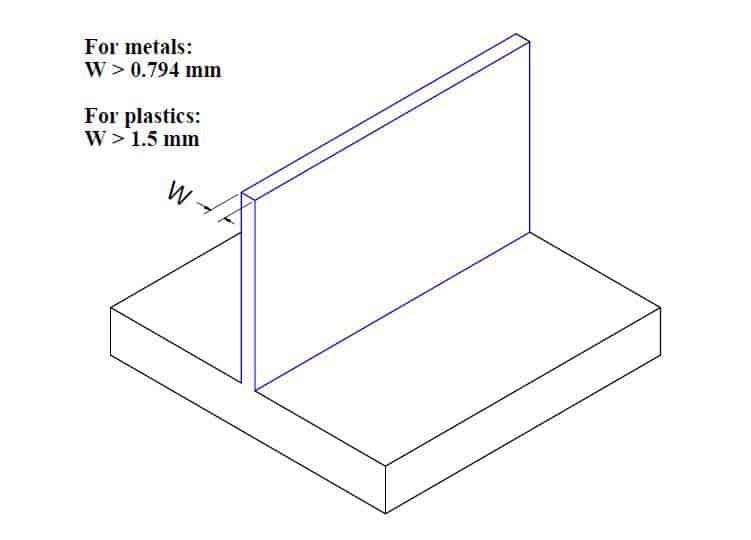
5. Des arêtes internes arrondies avec le bon rayon de courbure
Les outils de découpe étant cylindriques, il est impossible d’usiner des arêtes internes parfaitement à angle droit. La seule façon d’y parvenir est d’avoir recours à un procédé d’électroérosion (EDM), ce qui est beaucoup plus onéreux. C’est pourquoi nous recommandons que toutes les arêtes internes de votre ouvrage soient arrondies, ce qui évitera au banc d’usinage de perdre du temps à essayer de réaliser un angle droit. En ce qui concerne le rayon de courbure, nous recommandons au minimum 1/3 de la profondeur de cavité. Un rayon plus réduit demandera l’utilisation d’un outil de diamètre plus faible, ce qui le rendra incapable de retire toute la matière en une seule passe. L’outil devra donc s’y prendre à plusieurs reprises et à vitesse réduite, ce qui augmentera les temps d’usinage et les coûts de fabrication.
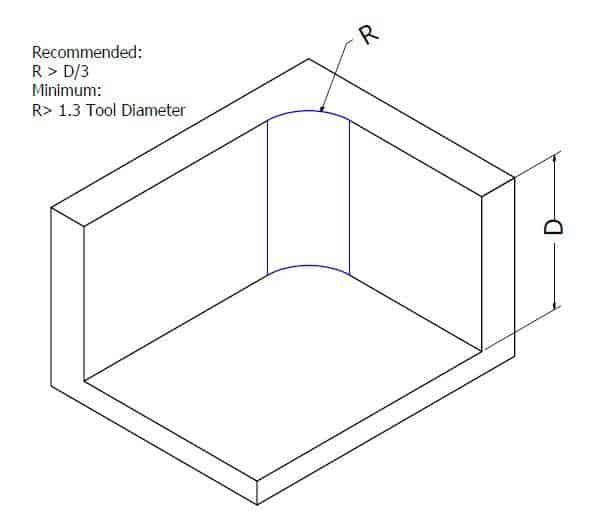
6. Limiter la profondeur de cavité
La réalisation de cavités profondes demande beaucoup de temps car elle implique d’enlever beaucoup de matière. Le procédé peut aussi entraîner certains problèmes (collision avec le mandrin, déviation ou casse de l’outil de découpe) que l’on ne peut éviter qu’en abaissant progressivement la mèche, ce qui représente une perte de temps considérable.
Le meilleur moyen de s’affranchir de ces contrariétés consiste à limiter la profondeur des cavités à usiner à 4 fois leur largeur. Par exemple : une cavité de 10 mm de large ne devra pas excéder une profondeur de 40 mm. À noter que l’on considère comme profonde toute cavité dont la profondeur est six fois supérieure au diamètre de l’outil de découpe.
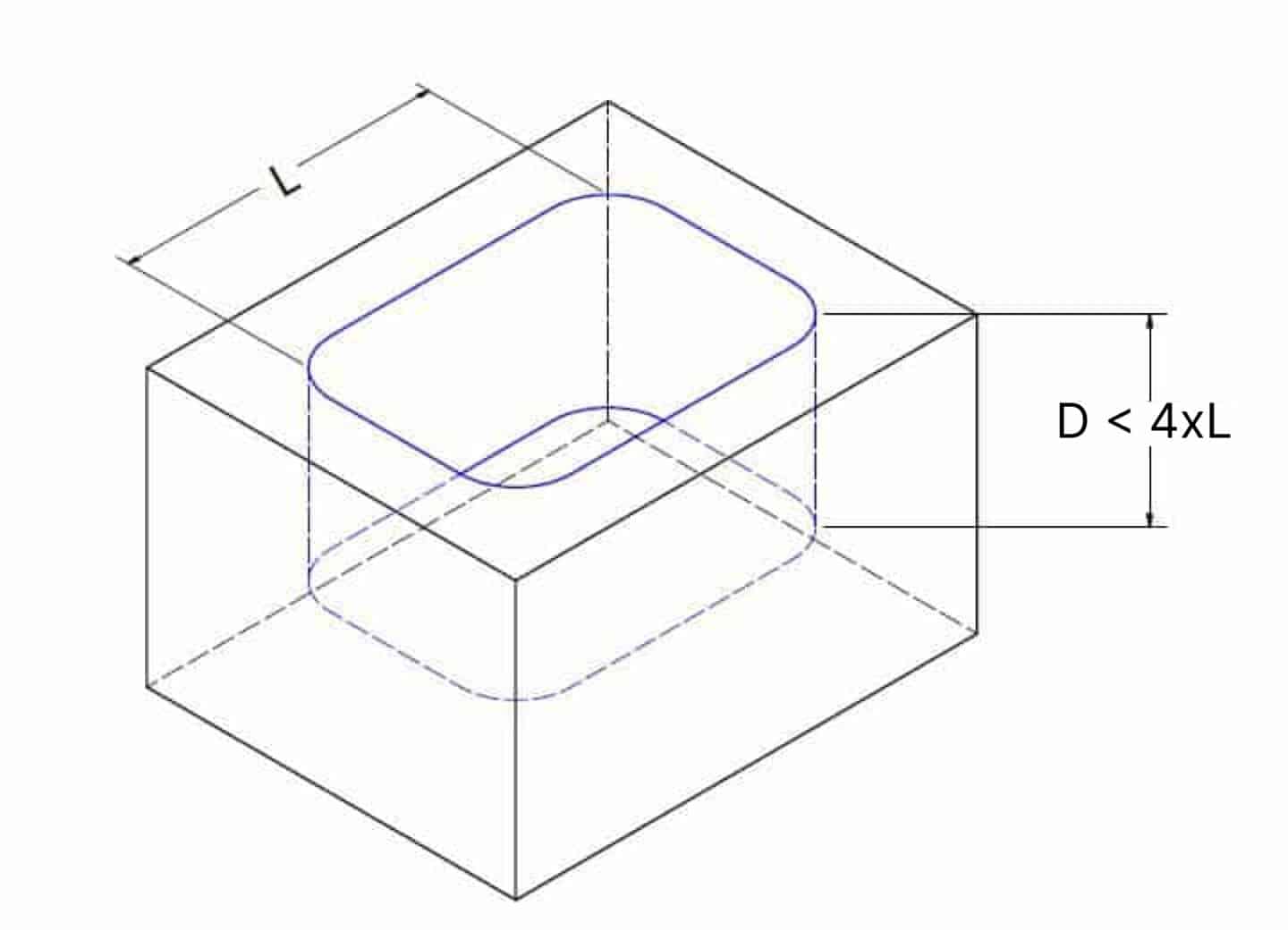
7. Limiter la profondeur des filetages
Les filetages fournissent des connections très fiables mais dont la force ne dépend que des premiers tours. Par conséquent, les filetages longs ne sont pas nécessaires. De plus, les longs filetages demandent l’utilisation d’outils spécifiques, en plus d’être plus long à usiner et de demander plus d’efforts. Efforcez-vous de limiter la profondeur des trous taraudés à trois fois leur diamètre. Dans le cas des trous taraudés borgnes, nous recommandons d’ajouter une longueur non filetée dans le fond du trou, d’au moins la moitié de son diamètre.
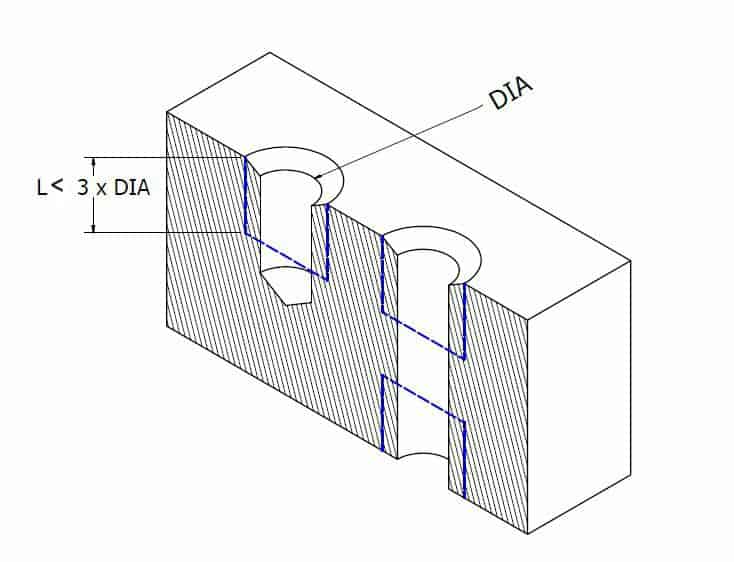
8. Spécifier les tolérances que lorsque c’est nécessaire, et éviter les tolérances trop serrées
Les tolérances peuvent rapidement faire monter les coûts de fabrication et ne devraient donc être spécifiées que lorsque c’est absolument nécessaire. Les machines CNC font déjà preuve d’une grande précision et se conforment à des tolérances normalisées tant que des tolérances sur mesure ne sont pas spécifiées dans l’ouvrage. En raison de la difficulté à les respecter, les tolérances serrées ne doivent être spécifiées qu’en cas d’absolue nécessité. De plus, elles rallongent le temps d’usinage et compliquent le processus de vérification manuelle. Nous recommandons aussi l’utilisation du système de cotation et tolérancement géométrique (GD & T), qui définit des tolérances plus relâchées, sur tous vos plans et esquisses.
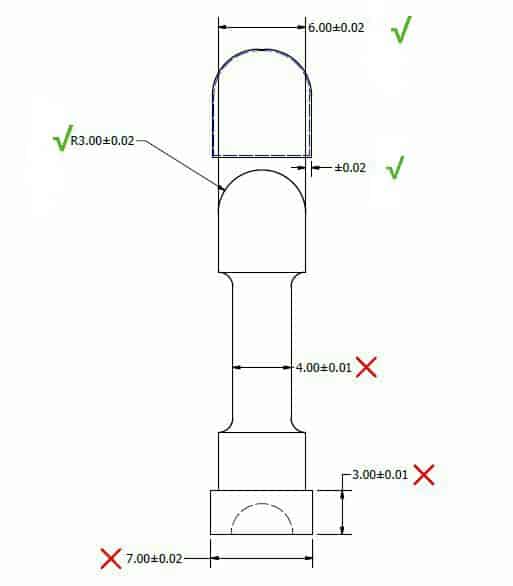
9. Utiliser des tailles de trou standards
Au moment de concevoir vos trous, pensez à les définir en fonction des tailles de mèche standards. Des trous de taille hors-norme devront de toute façon être réalisés à l’aide de mèches plus petites qui devront donc usiner les flancs en plusieurs passes, ce qui augmentera le temps de fabrication.
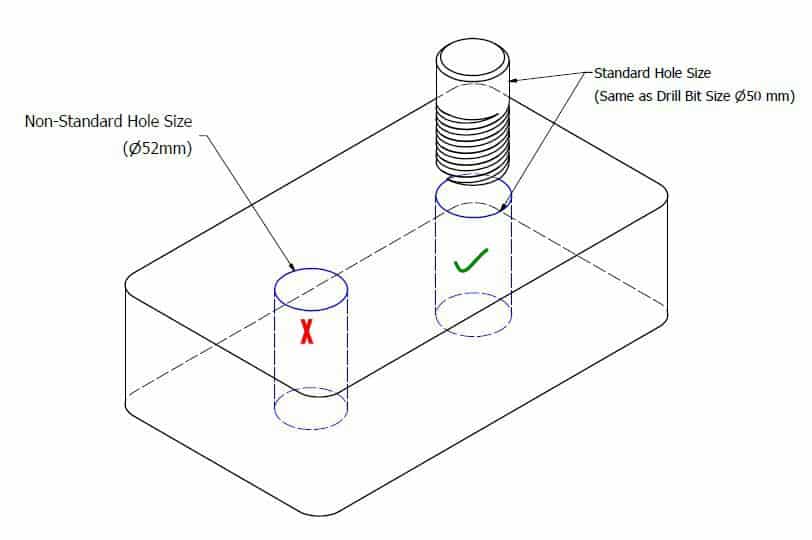
10. Ne pas inclure de texte à usiner
Usiner du texte est superflu, en plus d’être coûteux. Si nécessaire, le texte voulu pourra être peint sur la pièce une fois achevée. Si malgré tout il est nécessaire d’inclure du texte à usiner, préférez la gravure car elle implique moins d’enlèvement de matière.
Conclusion
En suivant ces quelques astuces, vous pourrez réduire le coût de vos pièces mécaniques usinées en CNC de façon significative. Xometry Europe vous propose des services d’usinage CNC rapides, fiables et bon marché, aussi bien pour les pièces uniques que pour les productions en grandes séries. Une fois votre modèle optimisé, importez-le sur notre plateforme de devis instantané et choisissez le matériau le plus approprié pour votre application.