Questo articolo mira a discutere i 6 errori principali che i progettisti CAD commettono quando progettano per il CNC e come evitarli. Prendendo nota di questi errori, è improbabile che sia necessario tornare alla tabella di progettazione, risparmiando così costi, tempo e risorse. Di seguito sono riportati i principali 6 errori nella progettazione CAD per la lavorazione CNC.
Le macchine CNC offrono a ingegneri e meccanici uno dei modi più semplici per creare parti in metallo e polimeri. Tuttavia, la creazione di disegni CAD per macchine CNC può essere piuttosto problematica. Richiede la massima concentrazione e vigilanza per evitare una produzione di parti difettosa, imprecisa o costosa.
Disegnare facce eccessivamente sottili
I progettisti spesso non tengono conto del possibile comportamento di un pezzo durante la lavorazione. Le proprietà del pezzo da lavorare sono un’altra considerazione importante: disegnare facce eccessivamente sottili è una delle conseguenze di queste dimenticanze.
Ad esempio, pareti sottili lavorate da un alluminio a bassa rigidità possono staccarsi o deformarsi durante un processo di fresatura a causa di vibrazioni eccessive. Riducendo lo spessore della faccia si riduce la rigidità del materiale, aumentando così le vibrazioni durante la lavorazione e abbassando la precisione raggiungibile. Un modo per superare questo problema è quello di mantenere un basso rapporto tra altezza faccia e spessore (H:S) e altezza faccia e lunghezza (H:L) quando si disegna una sezione di faccia sottile. Per avere un’idea di standard industriale non ufficiale, lo spessore minimo di una faccia è di 0,794 mm.
Tuttavia, le facce sottili sono molto spesso un requisito di progettazione. In questi casi, è più economico impiegare altri metodi di produzione come l’utilizzo delle lamiere.
Progettare caratteristiche che sono impossibili da lavorare
Non tutte le caratteristiche progettabili su un software CAD possono essere lavorate in modo efficiente da una macchina CNC. Una di queste caratteristiche da evitare nella progettazione per CNC sono i fori con percorsi curvi. Indipendentemente dal grado di libertà che può essere raggiunto da una macchina CNC, essa non può lavorare efficacemente un foro curvo.
Se questa caratteristica è necessaria per il vostro componente, può essere utilizzato un metodo noto come elettroerosione (EDM). L’EDM è un processo in cui la forma desiderata viene creata mediante scariche di corrente.
Uso eccessivo delle tolleranze
Le tolleranze definiscono gli intervalli di una dimensione accettabile. Esse variano a seconda delle macchine. Molti progettisti CAD progettano lavorazioni CNC senza una conoscenza generale delle tolleranze della macchina per la quale stanno disegnando. Questo riduce la qualità del pezzo lavorato. È fondamentale rimuovere le tolleranze inutili da un progetto in base alle caratteristiche della macchina utilizzata.
Anche per macchine CNC di alta qualità, tolleranze troppo strette nella vostra progettazione possono essere costose. Non tutte le superfici di un pezzo richiedono tolleranze. Evitate di assegnare a tali superfici, come raggi e diametri, delle indicazioni numeriche sul vostro disegno.
Progettare caratteristiche estetiche non necessarie
Al fine di risparmiare costi e tempi di progettazione per la lavorazione CNC, è necessario considerare la quantità di materiale da rimuovere e il processo da utilizzare per farlo. Domande come “è necessario rimuovere il materiale per un semplice aspetto estetico?” e “è assolutamente necessario aggiungere un’unica caratteristica complessa, che richiede una lavorazione a 5 assi alla progettazione” dovrebbero essere prese in considerazione da un progettista quando si progetta per il CNC.
Si dovrebbero evitare inutili asportazioni di materiale e considerazioni di carattere estetico. Invece di lavorare a macchina per fini di estetica, si possono utilizzare processi di post-lavorazione come l’elettrolucidatura.
Progettazione di cavità troppo profonde
Gli utensili CNC hanno una lunghezza di taglio limitata. Gli utensili di fresatura sono tipicamente più efficienti quando le cavità di fresatura raddoppiano o triplicano il loro diametro in profondità. Ad esempio, una fresa da ø15mm taglia in sicurezza cavità fino a 35 mm di profondità. La fresatura di cavità profonda può causare l’incapacità dell’utensile di raggiungere la superficie da fresare, la deflessione dell’utensile causata dall’eccessiva sporgenza di un utensile dalla pinza, la frattura dell’utensile e la difficoltà di evacuazione del truciolo. Per superare queste problematiche, è necessario fare quanto segue:
1) Abbassare progressivamente la fresa con incrementi sempre più piccoli.
2) Utilizzare un utensile da taglio sufficientemente grande o un portautensile più lungo. In questo modo si risolvono i problemi dello sbraccio e della deformazione dell’utensile.
3) Utilizzare il liquido di raffreddamento ad alta pressione per rimuovere efficacemente i trucioli della macchina.
4) Utilizzare altre forme di lavorazione come l’elettroerosione.
Progettazione di angoli interni senza raccordi
Gli utensili di fresatura CNC sono di forma cilindrica. Di conseguenza, questi utensili creano sempre un raggio per la fresatura di bordi verticali interni. È un errore comune quando si disegna per la lavorazione CNC progettare spigoli vivi per angoli interni. Siccome la macchina creerà automaticamente un raggio, è meglio includerlo nel progetto.
Quando si progettano tasche rettangolari profonde, assicurarsi di aggiungere un raggio d’angolo di almeno ⅓ rispetto alla profondità della tasca. Gli spigoli vivi o i raggi angolari non sufficientemente grandi richiedono utensili di diametro molto più piccolo a velocità inferiori, aumentando così i costi e i tempi di lavorazione.
Inoltre, il raggio dell’utensile da utilizzare nella lavorazione a macchina deve essere preso in considerazione quando si progetta un raggio dello spigolo. Il raggio dello spigolo dovrebbe essere un po’ più grande del raggio dell’utensile di fresatura. Questo permette all’utensile di tagliare a velocità più elevate e riduce anche lo stress sull’utensile.
Se il vostro progetto richiede angoli interni a spigolo vivo, come ad esempio cavità in cui deve essere inserita una parte rettangolare, è meglio progettarne le cavità interne con gole di scarico (seconda immagine).
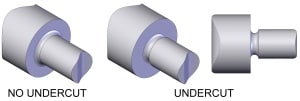